The round becomes the square
Chop, chop, chop, 120 beats per minute, a hefty noise and flickering lights, but by no means a techno party: the beat is provided by automatic welding grid machines, short-circuit currents provide the "lightshow". Every half second, transverse and longitudinal wires are welded together to form a complete industrial mesh, or in other words, wire is processed with high-tech in Wegberg in the Lower Rhine region.
And yet it is a 'hot dance' in the truest sense of the word that the 35 employees at Kaufmann & Lindgens in Wegberg perform every day and around the clock. This is because spot-welded grilles have been produced for over 50 years using electrical resistance welding, similar to projection welding in car body construction. Under the welding portal of the semi-automatic machines, a short-circuit current heats the wire material at the crossing points to over 900 0C in a fraction of a second. The material is then joined by simultaneous compression, followed by water-cooled hardening of the spot weld.
The automation of this joining process - without the addition of a filler material - was initially driven after the Second World War by the production of reinforcing steel mesh, the use of which revolutionised installation practice in the construction industry at the time. Standardised mats with large mesh widths, thick wires and panel sizes of 6 x 2.5 m could be produced quickly, precisely, cleanly and with reproducible quality. The faster, the more cost-effective.
Over the decades, further developments in the electrical, mechanical and control technology fields ensured that ever thinner wires, smaller mesh sizes and tighter tolerances could be realised. The market for welded mesh became established, round-drawn smooth wires with a chrome-platable surface found their way into mass production and industrial mesh developed as a lightweight steel construction element between demanding requirements and technical feasibility. Today, bright, galvanised or stainless steel wires from 2.0 mm diameter are welded, mesh widths of 20 mm and less are realised. Accurate to the millimetre, tension-free, flat. A standard mesh with a pitch of 25 mm and a wire thickness of 3.0 mm has long been part of the delivery programme of a high-performance industrial mesh manufacturer in the 3x1.5 m panel size.
Spot-welded wire mesh is used in a wide variety of areas: as protective fencing, gravel cages, cable ducts, in transport containers, goods presentation systems, as façade panelling, railing infill, ceiling suspension, animal cages, barbecue grids, shopping trolleys, fall protection, cargo space partitioning, etc. Depending on the product, the requirements for welding quality, tolerances or external shape vary greatly. In addition, the market for industrial mesh demands maximum flexibility and cost-effectiveness, for mass production as well as for batch size 1.
There are basically two different methods for feeding longitudinal and cross wires in the production of industrial mesh with wire thicknesses of 2.0 to 8.0 mm: continuous welding from a spool and the manual or automatic feeding of pre-straightened and pre-cut bars. The former method is particularly worthwhile for high and very high quantities, as it can sometimes take days just to set up such a system for a different product. In addition to the space required for such a machine - each longitudinal wire comes from a different reel - there are sometimes also qualitative disadvantages, e.g. a lack of flatness. On the other hand, thinner wires in particular can be handled better in the feed and additional necessary finishing processes, such as trimming or notching, can be integrated more economically.
Welding "from the bar", on the other hand, offers greater flexibility thanks to shorter changeover times and, in addition to thicker wires, flat bars or pre-bent frame wires, for example, can also be fed to the welding portal without any problems.
In the race for ever greater output and constantly increasing cycle times, machines with combined feeding technology are now becoming established: the cross wires are straightened/cut to length directly at the welding portal and then "shot in", sometimes on both sides or from above and below (e.g. in the production of double-bar fence elements).
Not only does the control technology, which can be called up and programmed directly on the machine terminal via a user-friendly touch screen, have to be designed for these high speeds, but the corresponding performance and power of the welding transformers and presses, the precise cooling and the exact feeding and positioning of line and cross wires would have been unthinkable in this form 15 years ago. With a 2 metre wide grid with a mesh width of 40 mm, 1 cross wire is welded simultaneously with 50 line wires, 2 of which are welded on or under 1 copper electrode, 2 electrodes per electrode holder, 2 holders per welding transformer, up to 10 transformers on one machine. The entire assembly has to withstand a pressing pressure of up to 5 kN, twice per second. This alone is a precision engineering challenge for the designer and setter/operator of the appropriately designed semi-automatic or fully automatic machines. The careful selection and harmonisation of the optimum materials and components used is a science in itself. When selecting the shape, geometry, thickness/mass, accuracy of fit, hardness and electrical conductivity of the most suitable copper electrodes alone, there are hundreds of possible combinations; and yet deformations and burnt residues quickly form on the electrode surface, which have to be removed again and again.
In Wegberg, a careful production planning process ensures cost-effective production. It all starts with wire straightening, so orders of the same wire thickness and type are sequenced in such a way that the straightening and cutting systems have to be converted as little as possible. This is because each wire diameter requires different feed and pressure rolls, different bush sizes on the shearing blade and up to 5 straightening blocks that can be individually positioned within the rotating straightening blade. Straightening stones made of grey cast iron or hard metal, plastic or sometimes even wood, adapted to the respective wire thickness, of course.
Wire coils with a weight of up to 2 to. (that's a good 20 kilometres of 4.0 mm round wire!) are straightened without interruption. This type of coil preparation not only saves money in purchasing, but also so much time that one employee can operate, supply and dispose of 8 straightening and cutting machines at the same time. Driven unwinding discs, servo drive motors and an in-house developed stop system for cutting release guarantee straight bars and length tolerances of a few tenths of a millimetre at throughput speeds of up to 2 m/sec.
The rods produced in this stress-free manner and collected in collecting troughs on the straightening machine are fed in crane bundles to the longitudinal or cross wire magazines of the automatic welding mesh machines. Each line wire requires its own feed chute, copper electrodes arranged precisely underneath it and the most favourable positioning of the pull-out hooks on the pull-out side. These are pneumatically controlled and arranged on a pull-out carriage driven by a servomotor, which ensures that the cross wire pitch is fed with an accuracy of one tenth of a millimetre. Different mesh sizes require different electrode widths, the amount of current, pressure and welding time varies depending on the wire thickness and quality, and the appropriate combing wheels and positioning units for the cross wire also need to be installed. Finally, the welding transformers, which are generally based on alternating current technology, always require both poles and opposite poles (plus/minus), i.e. ideally an even number of longitudinal rods. Ten years ago, a simple change of mesh width could quickly mean up to 8 hours of conversion time; today it is still 4 hours on average. And time is money, because ultimately the value chain from wire to finished industrial mesh is more than manageable. The market predominantly determines the price of the finished mesh; the quality of the welding, flatness or compliance with dimensional tolerances are assumed by customers.
Consequently, the right sequence planning is also important on the welded wire mesh machines, as the "sequencing" of orders with the same mesh size and wire thickness, for example, can reduce the scope and time required for conversions and minimise the necessary downtime costs. Well done to the manufacturer who has a large and flexible machine park, a sufficient order backlog and their own standard mesh programme.
The latter also offers additional economic benefits for small batch sizes: individual or sample meshes can be cut from stock and passed on to the customer quickly and cost-effectively. Although customised products are now also available at a reasonable price thanks to more flexible automatic welded mesh machines, the waiting time until it somehow "fits" can be up to 4 or even 6 weeks.
Those who can wait for this, on the other hand, benefit from the high level of automation in Wegberg: handling devices not only stack automatically, additional units installed also allow different wire thicknesses, shapes and lengths to be joined to the finished mesh under the welding portal, just as recesses or edge processing can be integrated. In many cases, this eliminates the need for subsequent and therefore additional processing steps.
If the required mesh geometry cannot be produced on an automatic machine or cannot be produced economically, a CNC-controlled coordinate welding machine is used. Here, the individual wire rods (also three-dimensionally bent or flat materials, etc.) are first inserted into a type of template, then a single electrode moves along the 2x1m working area and provides the necessary connection of the intersections. Nowadays, an inexpensive industrial mesh no longer necessarily has to consist of straight wire rods of one type running at right angles to each other.
It is not only the most favourable purchase price for wire that decides the weal and woe of an industrial mesh manufacturer (the material price often accounts for up to 70% of the sales price), but above all the short-term availability of the various required qualities (tensile strength, surface quality, material composition, etc.) is the decisive factor for survival on the market. Due to its susceptibility to corrosion, large quantities of wire cannot be stored for long, let alone financed, and the sharp fluctuations in steel prices over the last five years would also harbour an unacceptable risk of speculation. Close co-operation with a few well-stocked, efficient wire drawing mills is essential today. Short delivery times for wire mesh, perhaps the most important competitive advantage over the Far East apart from the quality aspect, can only be realised if the primary material wire is immediately available.
And finally, the "human factor" justifies Germany as a production location. After all, wire processing requires a great deal of dexterity. Only the intensive training and many years of experience of all employees in purchasing, planning and machine operation guarantee an efficient and adequate production process. A relatively high average age and many years of service are key indicators of personnel development at Kaufmann & Lindgens. In contrast, you will look in vain for any quality engineers in Wegberg, and there are just as few foremen or shift supervisors. Consequently, each machine operator is directly responsible for the quality of "his" welded mesh production; customer satisfaction is both a maxim and a motivation.
A welded mesh, for example, which at first glance appears to be a simple stitching together of round wires in fixed lengths, is actually a high-tech product whose series production requires a perfect mix of materials, machines and people. The proven technologies will continue to be developed further in the coming years. Not in principle, but in detail. Not higher, but faster. And further, in the sense of more precise, more level, more economical and more ecological. And perhaps the first high-tech party will even be held in Wegberg...
Volker Boos, Kaufmann & Lindgens GmbH for specialised journal „Draht“, Issue 01/2011
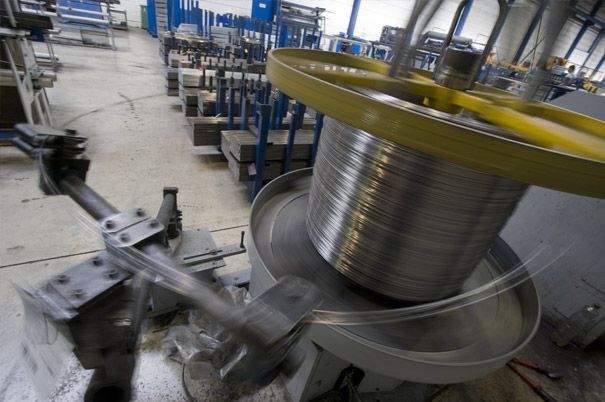




We get it done. Together.
Contact
Phone: +49 (0)2432 9889 - 0
Fax: +49 (0)2432 9889 - 48
E-Mail:
Web: www.schweissgitter.de